Source: The Conversation (Au and NZ) – By Krishanu Roy, Senior Lecturer in Engineering, University of Waikato
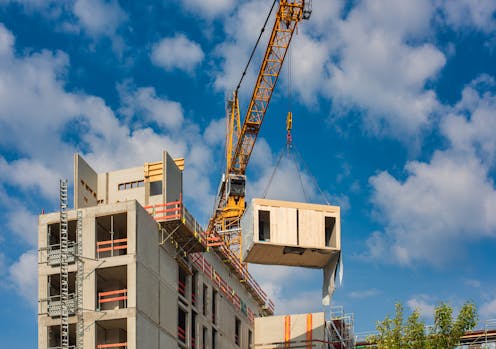
Getty Images
In the wake of Cyclone Gabrielle, New Zealand is again talking about “building back better”. But how do we build back better when we don’t necessarily understand what “better” means? Or how to achieve this across a country with significantly different risk profiles?
At its most basic level, build back better is an opportunity to rebuild homes and other buildings in a way that is responsive to future risks and sustainability needs. To achieve this, we need to address knowledge gaps around building within a circular economy. A circular economy is one that swaps the typical cycle of make, use, dispose in favour of re-using and recycling as much as possible.
A sustainable building in the circular economy model will minimise emissions and its impact on climate and natural resources across its entire life cycle. This life cycle includes the manufacturing of materials and construction, passive lifetime emissions, maintenance, as well as end-of-life requirements (deconstruction).
At the University of Waikato, our research is focused on material choices, both for long-term rebuild as well immediate emergency relief. We approach this from a structural engineering perspective and consider light steel, light timber, fiber reinforced polymers and concrete. We work alongside industry to develop know-how around deconstruction for light steel and timber structures.
The research will contribute to best practice guidelines and circular economy adaptation. Here’s why this is important.
Embracing a circular economy
The construction and demolition industry in New Zealand produces around 50% of all waste. According to the United Nations Environment Programme’s 2022 Global Status Report for Buildings and Construction, the sector accounts for more than 34% of energy demand globally and around 37% of energy and process-related carbon dioxide emissions. The report concludes that the building and construction sector are not on track to achieve decarbonisation by 2050 – the international deadline for achieving net zero energy emissions.
The New Zealand government has committed to the circular economy model in its plans to deal with waste.
Read more:
If companies want net-zero carbon offices,
they need to focus on building materials
But building back better isn’t simply about using sustainable materials and construction methods, and incorporating features that enable lower emissions during the “living phase” of a home.
Buildings need end-of-life considerations built into the design and construction, so they can be easily repurposed or deconstructed with minimal energy and then recycled, reused or disposed of in a manner that doesn’t send emissions through the roof.
Presently, we’re building sustainable homes on the premise of being carbon neutral by 2050, but they also need to be built on the premise of being carbon neutral at the end-of-life in 50 years.
We are not even close to achieving that. A report from building research institute BRANZ determined the climate impact of a new-build standalone house exceeds the 1.5℃ climate targets by a factor of 6.7 during its life cycle. This shows the substantial work needed to achieve carbon neutrality of new homes.
Modular buildings and new materials beckon
The solution to this issue may lie in modular homes and the development of new materials.
Quick and easy to make, modular homes provide fast options to house displaced people. They are also valuable for community wellbeing after the trauma of natural disasters. Finally, modular homes offer exciting opportunities for sustainability. They can be easily reconfigured to adapt to changing needs, for example, with the addition or removal of modules.
However, without careful design and know-how, modular homes and the foundations under them will not necessarily provide resilient and sustainable structures into the future.
The most challenging aspect of modular homes is the connection between the structures and their foundations. Therefore, it’s critical for resilient structures that the connections are designed carefully. Throughout the design process, those in charge need to consider the structure’s deconstruction or disassembly at the end of its life.
Read more:
How ‘net-zero’ and ‘passive’ houses can cut carbon emissions — and energy bills
That said, modular homes are also not the cure all for the entire building industry. The global need for sustainable and resilient buildings is a driver for the development of new construction materials, such as the plasterboard substitutes saveBOARD and Neocrete, a low-emission concrete.
These products offer low-emission building options, which use recycled materials in manufacturing and provide an alternative to high-emission materials. But, due to a lack of strict regulations around adopting new materials and a lack of awareness in the industry, adoption has been slow.
Identifying the missing data
In New Zealand, we have different risk profiles across the regions, depending on the likelihood of earthquakes and natural hazards like flooding, landslides, and wildfires – as well as the intensification of those hazards due to climate change.
The location risk profile dictates the best materials, but to utilise new materials, we need local testing data which are very limited as of yet.
Read more:
We can’t afford to just build greener. We must build less
If we’re really committed to building back better, then we need to do the research and incorporate the evidence into the building code, design standards and information for construction practitioners.
This could mean a “passport” for new materials based on local testing. The passport would incorporate details on the potential to recycle and reuse, a disassembly guide and a sustainability record (in essence, an environmental declaration).
The adaptation of the circular economy approach to the “build back better” strategy for buildings will be essential in reducing the risk of future catastrophes, as well as the impacts on climate and natural resources. Setting up a clear guideline for this strategy will be a pivotal early step in helping the industry define and oversee its efforts towards these objectives, which are currently lacking.
Krishanu Roy does not work for, consult, own shares in or receive funding from any company or organisation that would benefit from this article, and has disclosed no relevant affiliations beyond their academic appointment.
– ref. ‘Build back better’ requires a framework that focuses on the full life of a house – from materials to its end of life – https://theconversation.com/build-back-better-requires-a-framework-that-focuses-on-the-full-life-of-a-house-from-materials-to-its-end-of-life-203325